Iranian Art:Mina-kari
Enamel working and decorating metals with colorful and baked coats is one of the distinguished courses of art in Esfahan . Mina is defined as some sort of glasslike colored coat which can be stabilized by heat on different metals particularly copper.
Although this course is of abundant use industrially for producing metal and hygienic dishes, it has been paid high attention by painters, goldsmiths and metal engravers since long times ago. In the world, it is categorized into three kinds as below:
• painting enamel
• Charkhaneh or chess like enamel
• Cavity enamel.
What of more availability in Esfahan is the painting enamel of which a few have remained in the museums of Iran and abroad indicting that Iranian artists have been interested in this art and used it in their metal works since the Achaemenian and the Sassanid dynasties. The enamels being so delicate, we do not have many of them left from the ancient times. Some documents indicate that throughout the Islamic civilization of and during the Seljuk, Safavid and Zand dynasties there have been outstanding enameled dishes and materials.
Most of the enameled dishes related to the past belong to the Qajar dynasty between the years 1810 – 1890 AD.
There have also remained some earrings. Bangles, boxes, water pipe heads, vases, and golden dishes with beautiful paintings in blue and green colors from that time, Afterwards, fifty years of stagnation caused by the World War 1 and the social revolution followed. However, again the enamel red color, having been prepared, this art was fostered from the quantity and quality points of view through the attempts bestowed by Ostad Shokrollah Sani"e zadeh, the outstanding painter of Esfahan in 1935 and up to then for forty years.
Now after a few years of stagnation since 1992, this art has started to continue its briskness having a lot of distinguished artists working in this field. To prepare an enameled dish we should make the following steps: First, we choose the suitable dish by the needed size and shape which is usually made by coppersmith. Then, it is bleached wholly through enameled working which is known as the first coat. As the next step, it is put into a seven hundred and fifty – degree – furnaces. At this time, the enameled metal will be coated with better enamels for a few more times and is heated at suitable degrees. Now it is the turn of the painter to demonstrate his art. The Esfahanian artists, having been inspired by their traditional plans as arabesque, khataii (flowers and birds) and using fireproof paints and special brushes, have made painting of Esfahan monuments such as step, the enameled material is put into the furnace again and heated at 500 degrees. In this way, the enameled painting is stabilized on the on under – coat, so getting the special shining. Meanwhile, most of today"s enamel workings are performed on dishes, vases, boxes and frames in various sizes.
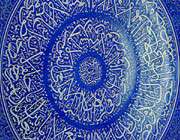
Other links:
Kamal-ol-Molk (A Great Master of Painting in Iran)
Kamal-ol-Molk’s experience abroad
Kamal-ol-Molks Style
Lithography in Iran (part 1)
Lithography in Iran ( part 2 )